Automotive & Mobility
Industry / Markets
In Germany in particular, the automotive sector has a very long tradition and a high status in industry and society.
KERATHERM® products from KERAFOL® are manufactured in accordance with the requirements of IATF 16949, the most important quality standard in the automotive sector.
This standard is specifically tailored to the automotive industry and contains important requirements for the quality management system, resulting in continuous improvement in the form of process improvements and the prevention of deviations and errors in the supply chain.
Even before receiving the certificate, KERAFOL® had long been active as a supplier to the automotive industry, even achieving the status of “preferred supplier” for one of the largest Tier 1s in the world.
KERAFOL® has been supplying Tier 1 and Tier 2 for many years in the form of products with “Made in Germany” quality.
The electrification of vehicles in particular brings with it many challenges, but also new fields of application. The electrified powertrain and the battery are the two core elements of an electric car. Due to the high power density and high performance requirements, weight, performance and thermal management play a major role here. The correlation between the temperature and service life of electronics has long been known, and the relationship between the temperature of a battery and the corresponding range of the vehicle and the maximum number of cycles is not surprising and is extremely important to understand and observe.
Battery and battery management system
(BMS)
The batteries in electric cars consist of many individual modules, which in turn are made up of many individual cells.
The design of the cell types ranges from prismatic and cylindrical to pouch cells.
Due to the high energy and power density, lithium-ion batteries are usually used.
The most common forms of cell chemistry in Germany are NMC (nickel, manganese, cobalt) or LFP (lithium iron phosphate).
NMC cells have a very good energy density and are very powerful.
However, they only work optimally at a “comfortable temperature”, which is why the cells require complex temperature control and are therefore relatively expensive.
The BMS also ensures efficient battery thermal management through intelligent control.
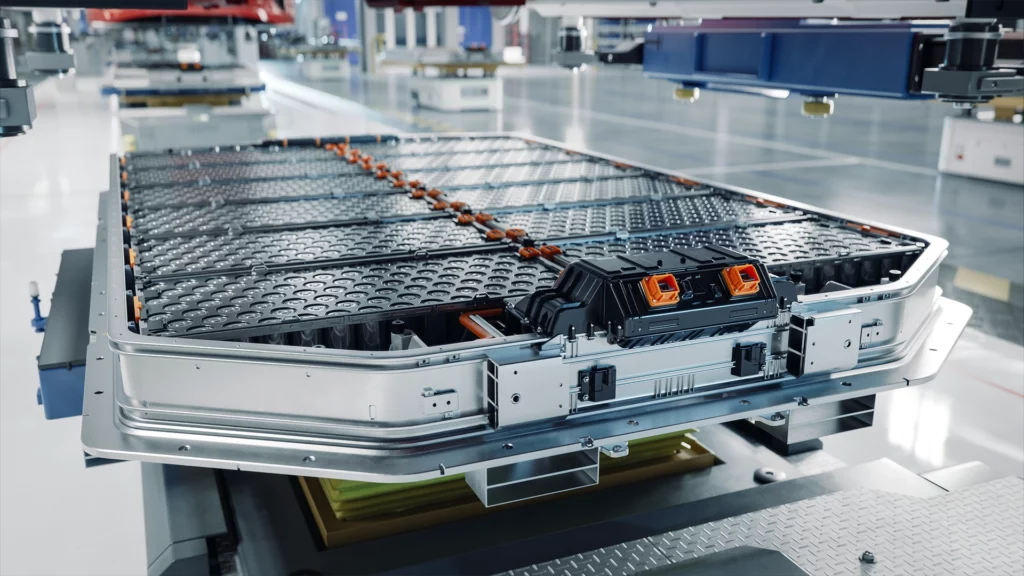
Video: Energy storage module
The BMS protects the battery against operating errors and enables optimum control of charging and discharging processes.
An active BMS relies on several components simultaneously and thus becomes a smart BMS.
It monitors the ageing and state of charge as well as the depth of discharge of the battery modules.
It controls the charging cycles intelligently and optimally with regard to speed, heat management or overcharging.
As both the battery and the BMS are the central components of the electric car, the range is still very broad in terms of technology and the materials used.
This in turn leads to a variety of different thermal management solutions that can be applied.
The most effective solution is to conduct the heat from the cells to the underside of the module and to use a thermal interface material between the module and the housing.
Due to the relatively large area that needs to be covered, gap filler liquids are the most common solution due to their good price/performance ratio and the ability to automate the application of the material using dispensing systems.
Case Study
Learn more about optimizing a battery management system (BMS) using the KERAMOLD® product range
Solutions
for battery and battery management system
Power Conversion
On Board Charger
(OBC)
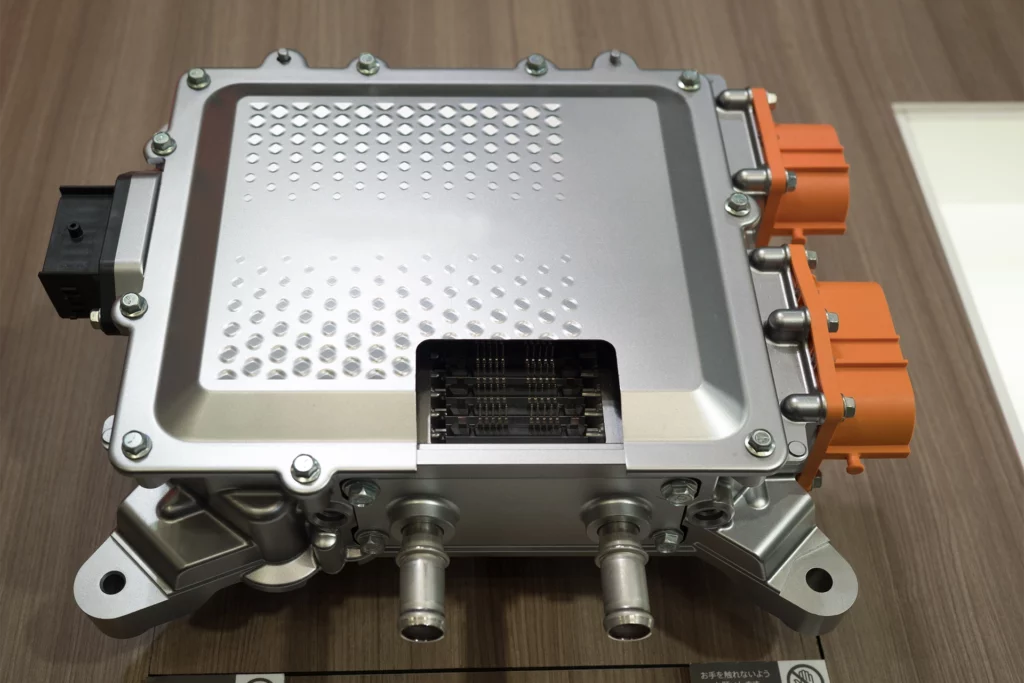
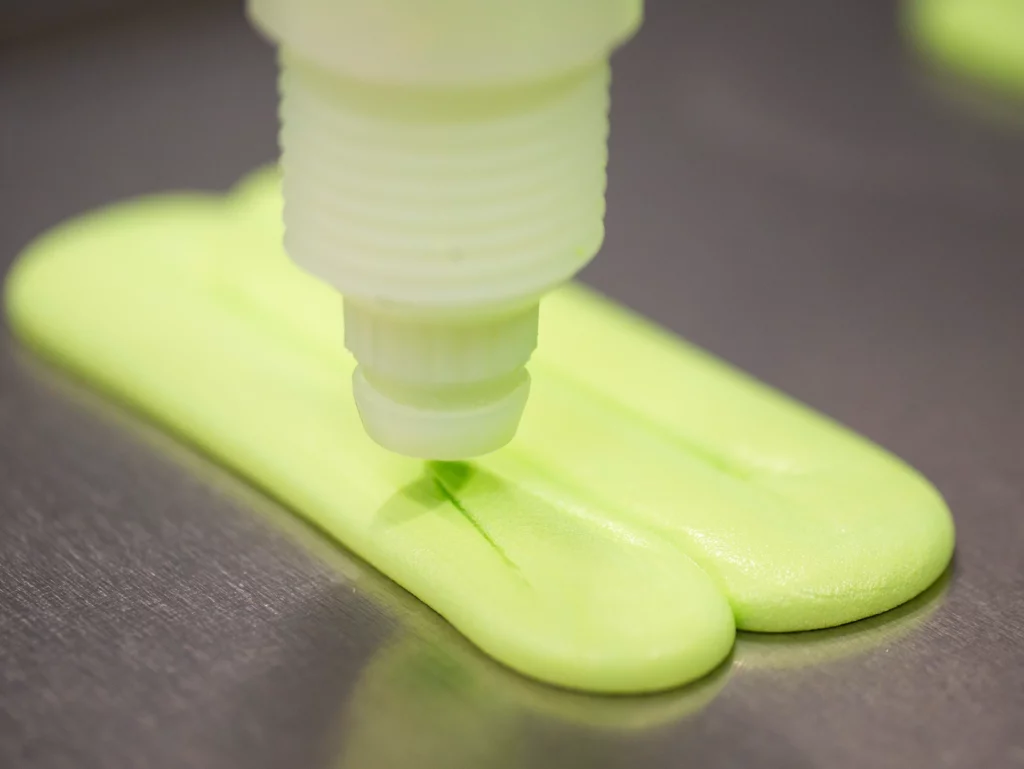
DC/DC Converter
Another component of the energy conversion systems in the electric car is the DC/DC converter. Converting the power of a high-voltage battery to a lower voltage level is necessary in order to supply all other consumers in the low voltage range (e.g. 12 V) of the car with energy, e.g. on-board computer or interior lights. A high level of heat is also generated in this assembly, which is dissipated towards the heat sink via thermal interface materials.
Inverter
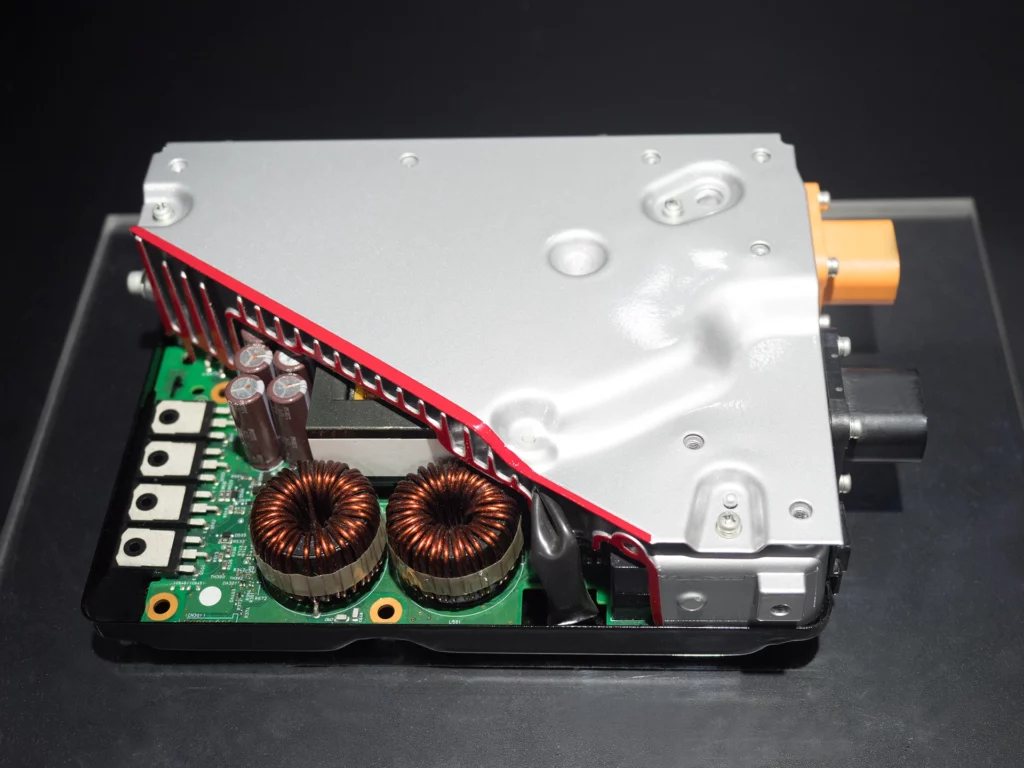
Solutions
for Power Conversion
Electric heaters
While vehicles with combustion engines have sufficient waste heat, electrically powered vehicles require an additional heating system. In addition to the high-voltage heater for the driver’s compartment itself, “electric auxiliary heaters” (12 V) are also used for the thermal management of the battery, an important component for reducing range loss.
German manufacturers are market leaders in the segment of high-voltage heaters, which are generally designed for a 400 V or 800 V architecture. Even if the concepts differ to some extent, in both cases the corresponding thermal management also determines the efficiency and reliability of the module.
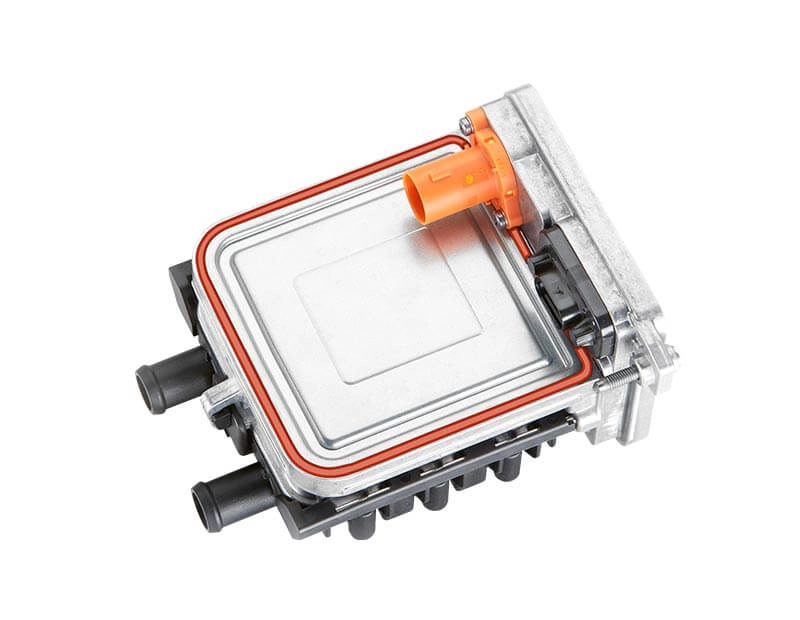
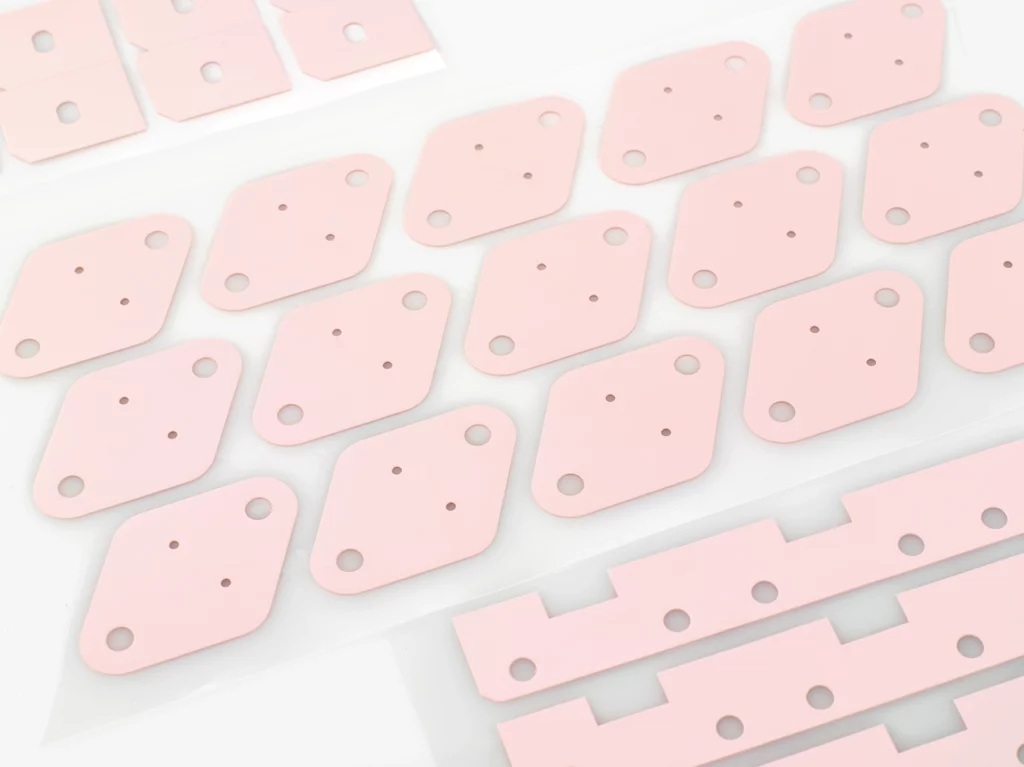
Solutions
for electric heaters
Products
eBikes
The electrification of bicycles offers many people a new form of mobility, both in everyday life and for leisure activities. In addition to the integration of the electric motor, the battery module including the intelligent battery management system (BMS), which protects the battery from damage, also plays a decisive role in terms of driving comfort. The requirements for the additional components are clearly defined:
- Low weight, low space requirement
- Energy efficiency - Long range
- High reliability and durability
- Quiet operation
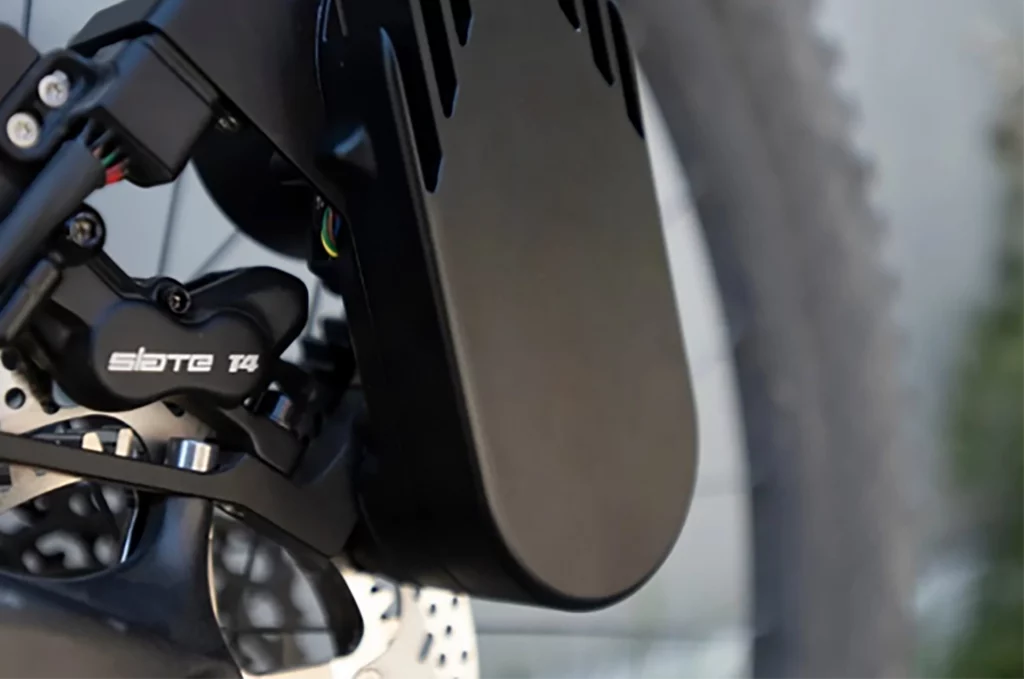
und Antrieb
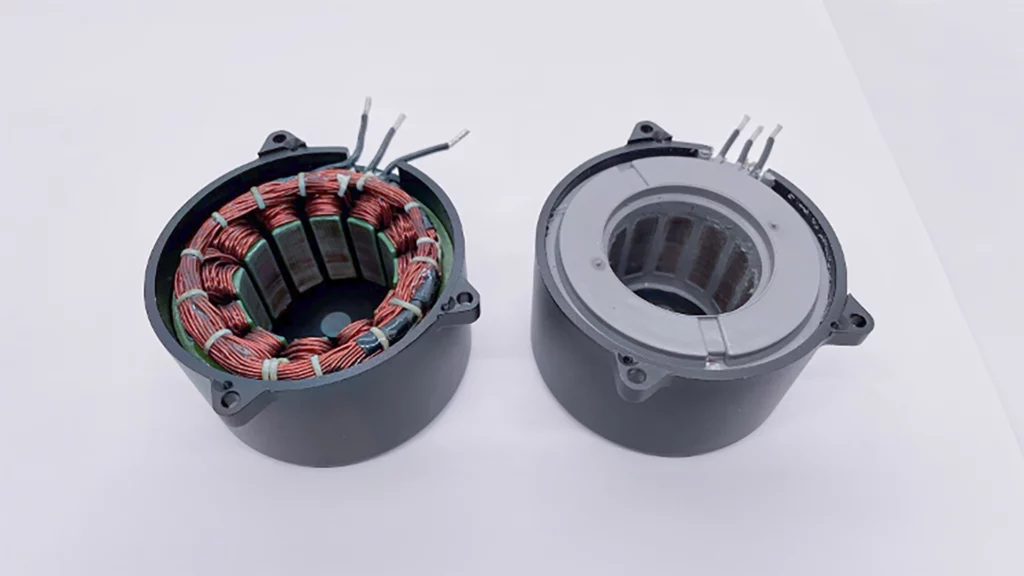
umspritzter Elektromotor
The battery modules from different manufacturers are very similar in design, mostly using so-called round cells. However, a closer look inside the battery module also reveals differences. On the one hand, there is the wiring, fixing and connection of the cells. While battery modules from older series still managed without the use of highly thermally conductive materials, the issue of thermal management has become increasingly important, partly due to the higher power density of the module. Instead of classic potting materials with a low thermal conductivity of 0.5 to 1.0 W/mK, gap filler liquids with a higher thermal conductivity of 1.5 to 3 W/mK are now increasingly being used to fill cavities between the battery cell and the housing. The lower thermal resistance can thus achieve better heat transfer, which protects the battery cells from overheating and can have a longer service life.
In many cases, a “conformal coating” has been applied to the BMS or PCB including the semiconductor to protect critical components from dust, dirt and moisture. Due to the higher performance requirements on the circuit board, an appropriate solution for heat dissipation is required. The products in the KERATHERM® range are helpful here. With these intermediate layer materials (Therma Interface Materials) in the form of foils or pads, the heat can be effectively conducted from the heat source to the heat sink (e.g. housing). Products in the KERAMOLD® series both protect the electronics (as in the case of conformal coating) and at the same time have the heat-conducting properties of a heat-conducting foil – an “all-in-one” solution.
The products in the KERAMOLD® series can also provide a truly innovative solution for electric motors. While electric motors have previously been encapsulated with low thermally conductive potting material, encapsulating them with thermally conductive injection molding granulate achieves the same effect, only with significantly increased thermal performance. Due to the softness of the polymer used, vibrations and noise can be compensated and dampened, which in turn increases drive comfort. The new gap filler range in the KERATHERM® series is also a more powerful alternative to conventional potting materials.
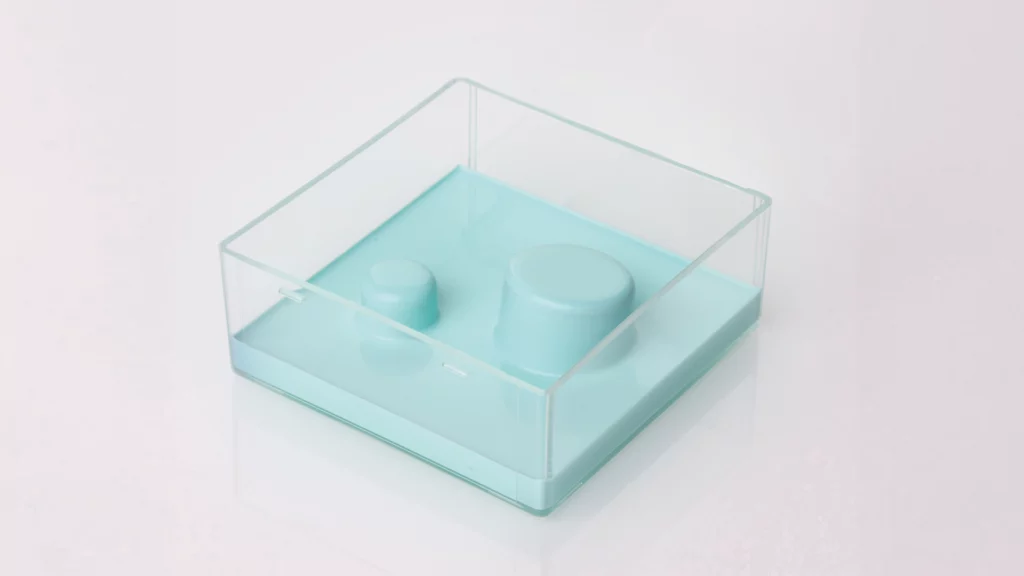
Case Study
Find out more about increasing the performance of an eBike electric motor using the KERAMOLD® product range
Solutions
for eBikes
LED
Vehicle headlights have changed visibly over the last 15 years, and for the better.
Whether in terms of pure radiance, energy consumption or technical solutions such as bend lighting – the use of LEDs has made these achievements possible.
The thermal management of LEDs is particularly important in terms of their sustainability.
This is due to the fact that individual LEDs and often the entire lighting unit cannot be replaced in the event of a failure.
This means that if the lighting unit fails, the entire assembly must be disposed of.
Even though LEDs are an efficient lighting solution, the energy density in a very small area is very high.
This makes it necessary to dissipate the heat generated locally.
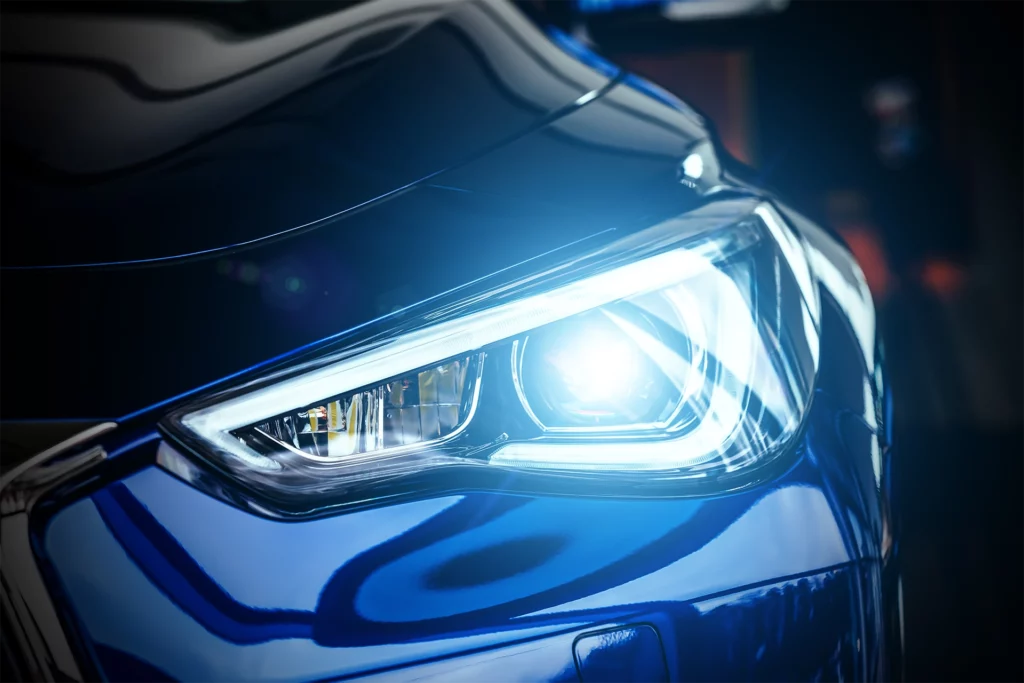
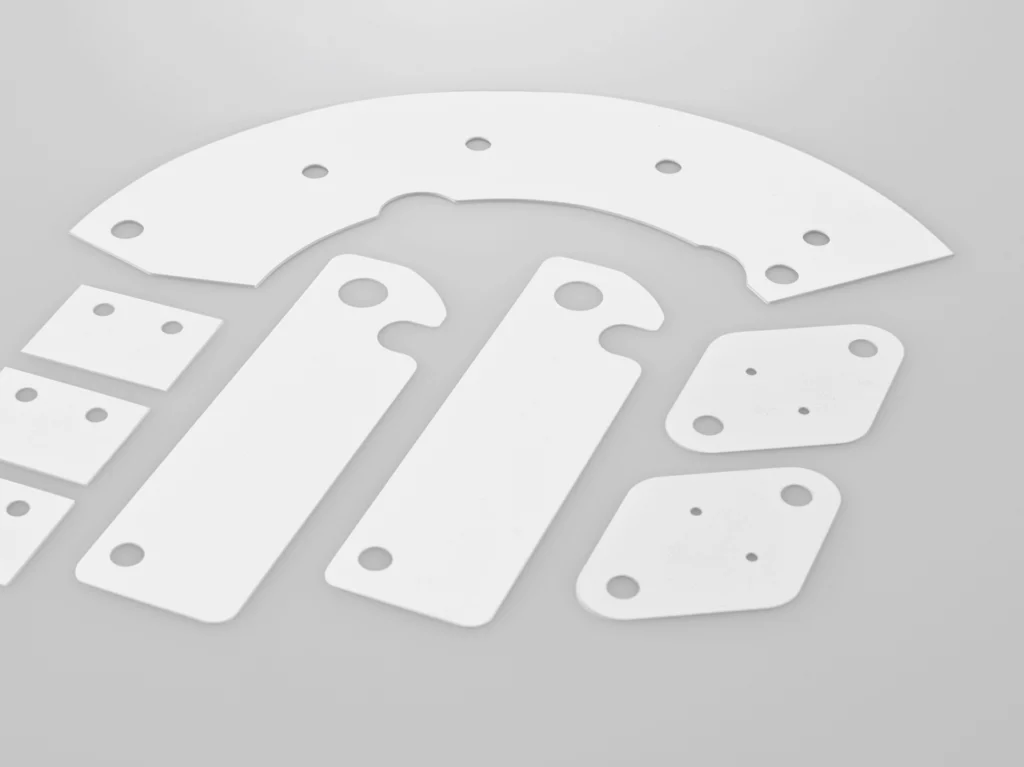