Injection molding
KERAMOLD®
The constantly increasing technical demands on electrical and electronic assemblies lead to major challenges in the area of thermal management. Due to the miniaturization of components and the higher performance of devices, component temperatures would increase significantly without countermeasures, which can lead to the failure of the entire assembly. In order to increase the longevity of electronic components, heat must therefore be conducted from the heat source (electronics) to the heat sink. Thermally conductive and electrically insulating intermediate layer materials, so-called thermal interface materials (TIMs), are used for this purpose. KERAFOL® has developed effective, uncomplicated and cost-effective solutions in this area with the KERATHERM® and KERAMOLD® product ranges. Thermal Grease is a product group that is also well-known in the consumer sector.

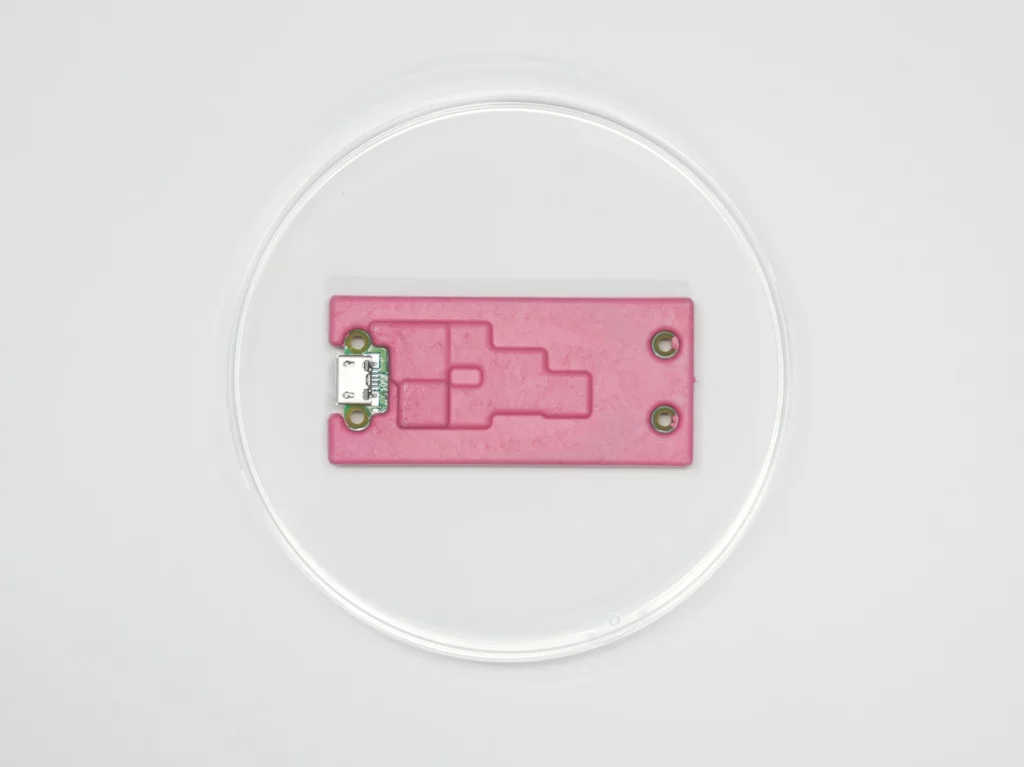
What is KERAMOLD®?
an explanation
In addition to conventional thermally conductive materials in the form of films, pads or gap fillers, KERAFOL® has also developed a thermally conductive injection-moulded granulate KERAMOLD® based on a TPE polymer (thermoplastic elastomer).
The new KERAMOLD® series enables 3D heat transfer and at the same time high electrical insulation of electronic components.
In addition, these components can be completely encapsulated/overmolded with thermally conductive materials using the “overmolding” process.
This means that electronic components can not only be cooled, but also protected from dust, moisture and mechanical influences – a real alternative to conventional encapsulation and potting materials due to the fast processing time.
Key Facts
to the injection molding of Kerafol®
- Thermoplastic elastomer
- Up to 2.5 W/mK
- Thermal conductivity: 3D instead of 2D
- High electrical insulation
- Very soft compared to other plastics (Shore A hardness range)
- Available as granulate or injection molded part
- Possibility to overmold components such as circuit boards in a pressure-friendly manner
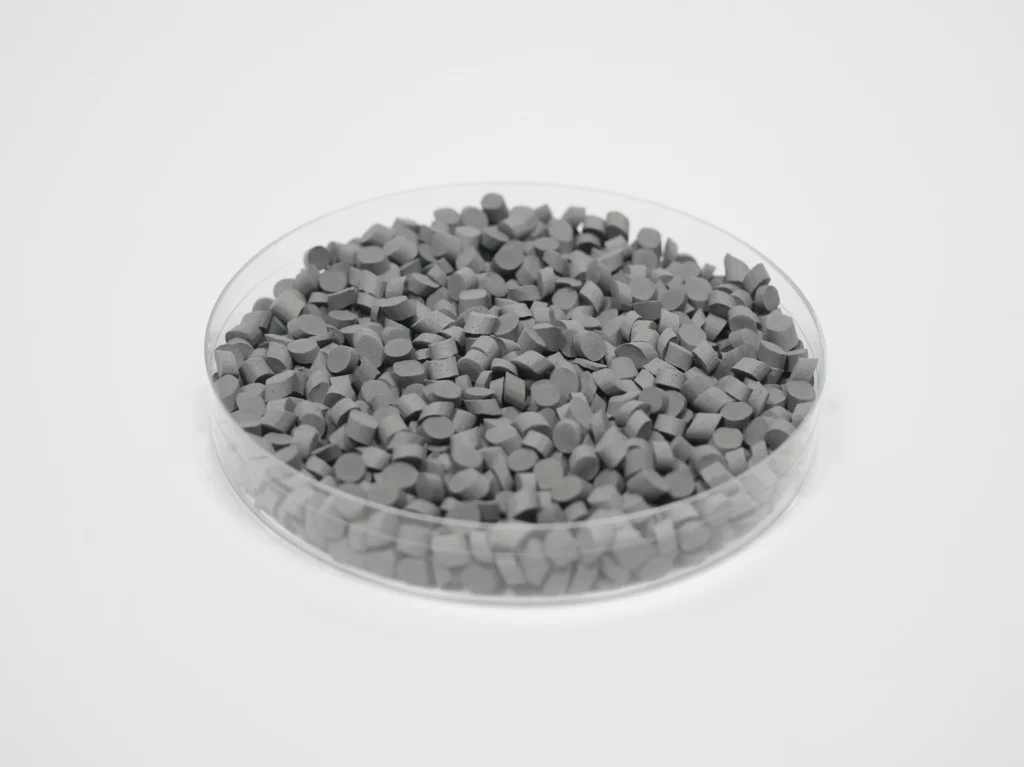
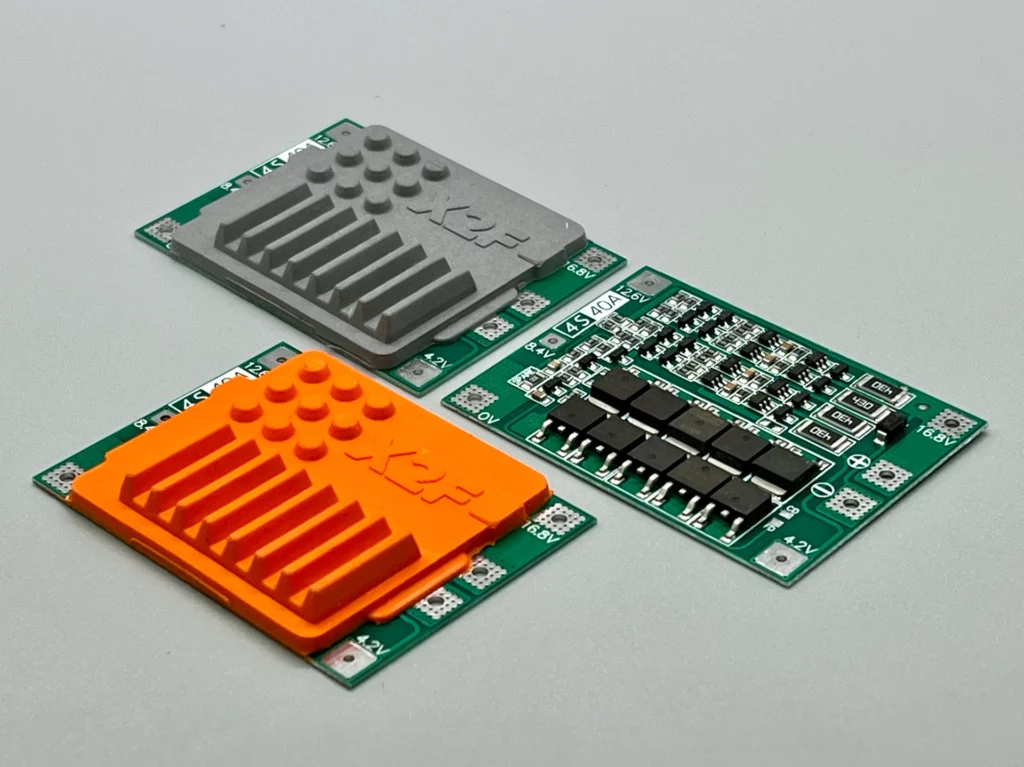
How to become KERAMOLD® materials processed?
Application
There are 2 different technical approaches for processing KERAMOLD®. On the one hand, the material can be processed using conventional injection molding machines. Various 3D geometries can be produced with the help of the individually manufactured injection molding tool. The processing conditions, such as pressure, depend on the system manufacturer, but the flowability of the KERAMOLD® series is generally very good despite the degree of filling.
Another material processing option is the so-called “overmolding” process.
With this process, assemblies can be completely or partially overmolded.
In order to avoid damaging sensitive electronic components during this process step, care is taken when designing the injection molding systems to apply the material at low pressure.
This is possible with KERAMOLD® materials thanks to the use of special polymers and fillers.
Further information on processing can be found in the Kerafol service section.
Video: Application
Advantages
of the KERAMOLD® product range
- Very high thermal conductivity in combination with high electrical insulation
- Compared to conventional injection molding materials, KERAMOLD is much softer, which results in better compensation of mechanical stresses and good contact with the surfaces
- Savings in production time compared to conformal coating or potting materials
- Alternative to potting materials
- Protection of electronic components from dust and moisture
- "All in one solution"
Delimitation
to other products
The main task of the Thermal Interface Materials Group is always the same – to combine the contrasting properties of thermal conductivity and dielectric strength.
In addition, both Gap Pads & Gap Filler Liquids and materials from the KERAMOLD® series are suitable for the mechanical requirement of bridging larger gaps and compensating for tolerances.
Nevertheless, there are various reasons why KERAMOLD® products are the preferred solution for certain applications and customer requirements.
The short processing time and the potentially high degree of automation are major advantages.
However, the uniqueness of this material lies in its ability to bond complex surfaces in the form of 3D parts efficiently and gently.
On the one hand, this enables very good heat transfer and, on the other, the assembly can also be encapsulated accordingly and thus protected from dust, moisture or mechanical influences.
This “all-in-one” solution means that other materials or production steps can be omitted (e.g. potting or conformal coating).
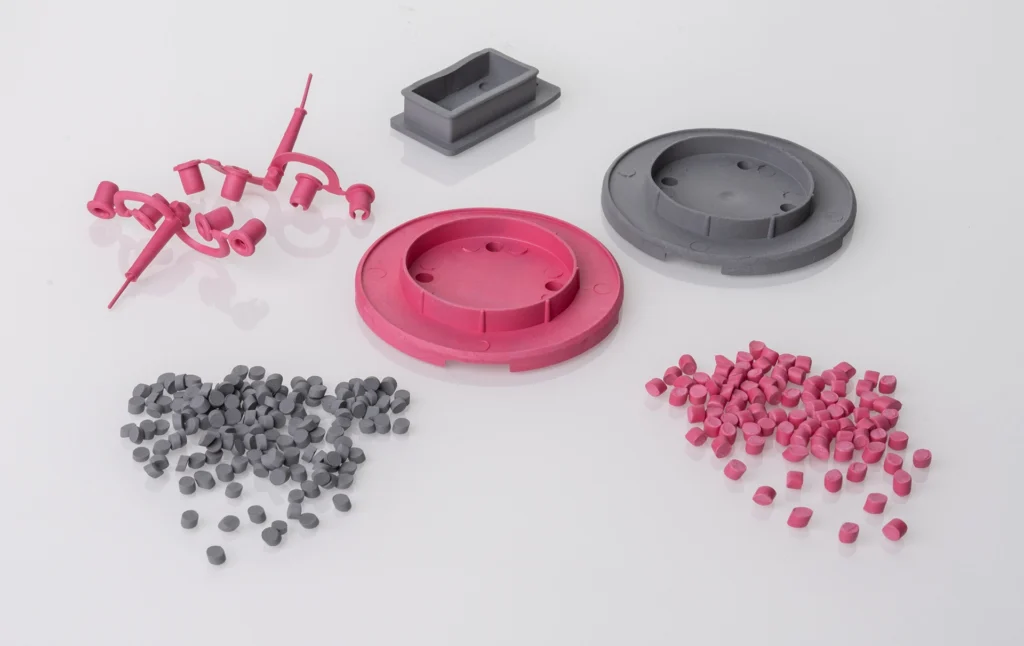
Comparison
KERAMOLD® products from Kerafol®
Applications
from KERAMOLD®
- Battery Management System (BMS)
- Electric motors
- Conductor rails
- Batteries
Of course, KERAMOLD® can also be used in many other electronic applications.
We would be happy to advise you on this to find the best solution for you.