Automotive & Mobilität
Industrie / Märkte
Gerade in Deutschland hat die Automotive-Branche eine sehr lange Tradition und einen hohen Stellenwert in Industrie und Gesellschaft. Die KERATHERM® Produkte von KERAFOL® werden gemäß den Vorgaben der IATF 16949, die wichtigste Qualitätsnorm im Bereich Automotive, gefertigt.
Diese Norm ist speziell auf die Automobilindustrie zugeschnitten und enthält wichtige Anforderungen an das Qualitätsmanagementsystem, wodurch eine stetige Verbesserung in Form von Prozessverbesserungen und Verhinderung von Abweichungen und Fehlern in der Lieferkette erfolgt.
Schon vor Erhalt des Zertifikats war KERAFOL® lange als Zulieferer der Automotive Branche tätig, bei einem der größten Tier 1 weltweit wurde sogar der Status „preferred supplier“ erreicht.
KERAFOL® versorgt seit vielen Jahren Tier 1 und Tier 2 in Form von Produkten mit „Made in Germany“ Qualität
Gerade die Elektrifizierung von Fahrzeugen bringt viele Herausforderungen, aber auch neue Anwendungsfelder mit sich. Der elektrifizierte Antriebsstrang und die Batterie sind dabei die zwei Kernelemente eines Elektroautos. Durch die hohe Leistungsdichte und hohen Leistungsanforderungen spielen hier Gewicht, Performance und auch Thermal Management eine große Rolle. Die Korrelation zwischen der Temperatur und Lebensdauer von Elektronik ist unlängst bekannt, der Zusammenhang zwischen der Temperatur einer Batterie und der entsprechenden Reichweite des Fahrzeugs sowie der maximalen Zyklenzahl ist nicht überraschend und äußerst wichtig zu verstehen und zu beachten.
Batterie und Batterie Management System
(BMS)
Die Batterien von Elektroautos bestehen aus vielen einzelnen Modulen, welche sich wiederum aus vielen einzelnen Zellen zusammensetzen. Die Bauform der Zelltypen reicht von prismatischen, zylindrischen bis hin zu Pouch-Zellen. Aufgrund der hohen Energie- und Leistungsdichte werden meist Batterien auf Lithium Ionen Basis verbaut.
Die in Deutschland am häufigsten vorkommenden Formen der Zellchemie sind NMC (Nickel, Mangan, Kobalt) oder LFP (Lithium-Eisenphosphat). NMC-Zellen haben eine sehr gute Energiedichte und sind sehr leistungsfähig. Sie arbeiten aber nur bei „Wohlfühltemperatur“ optimal, weswegen die Zellen aufwendig temperiert werden müssen und dadurch relativ teuer sind.
Das BMS sorgt dabei durch eine intelligente Steuerung auch für ein effizientes Battery Thermal Management.
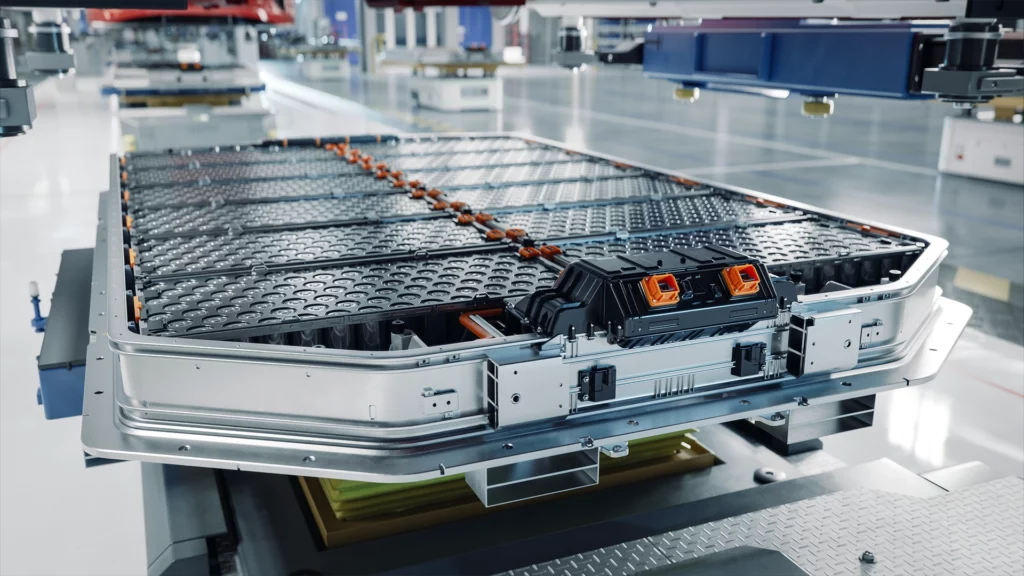
Video: Energiespeichermodul
Durch das BMS wird der Schutz der Batterie vor Fehlbedienungen sowie die optimale Aussteuerung von Lade- und Entladeprozessen ermöglicht. Ein aktives BMS setzt dabei auf mehrere Komponenten gleichzeitig und wird so zu einem smart BMS. Es überwacht Alterungs- und Ladezustand sowie Entladungstiefe der Batteriemodule. Es steuert die Ladezyklen intelligent und optimal hinsichtlich Geschwindigkeit, Wärmemanagement oder Überladung.
Da es sich sowohl bei der Batterie als auch bei dem BMS um die zentralen Bestandteile des Elektroautos handelt, ist das Angebot im Bezug auf die Technologie und der eingesetzten Materialien noch sehr breit gestreut.
Das wiederum führt zu einer Vielzahl verschiedener Thermal Management Lösungen, die angewandt werden können. Die effektivste Lösung besteht darin, die Wärme der Zellen an die Unterseite des Moduls zu leiten und ein Wärmeleitmaterial zwischen dem Modul und dem Gehäuse zu verwenden, ein sogenanntes Thermal Interface Material. Aufgrund der relativ großen Fläche die dabei abgedeckt werden muss, sind Gap Filler Liquids aufgrund ihres guten Preis-/Leistungsverhältnisses und der Möglichkeit, das Auftragen des Materials mit Hilfe von Dispensanlagen zu automatisieren, die gängigste Lösung dafür.
Case Study
Erfahre mehr über die Optimierung eines Batterie Management Systems (BMS) mithilfe der KERAMOLD® Produktreihe
Lösungen
für Batterie und Batterie Management System
Power Conversion
On Board Charger
(OBC)
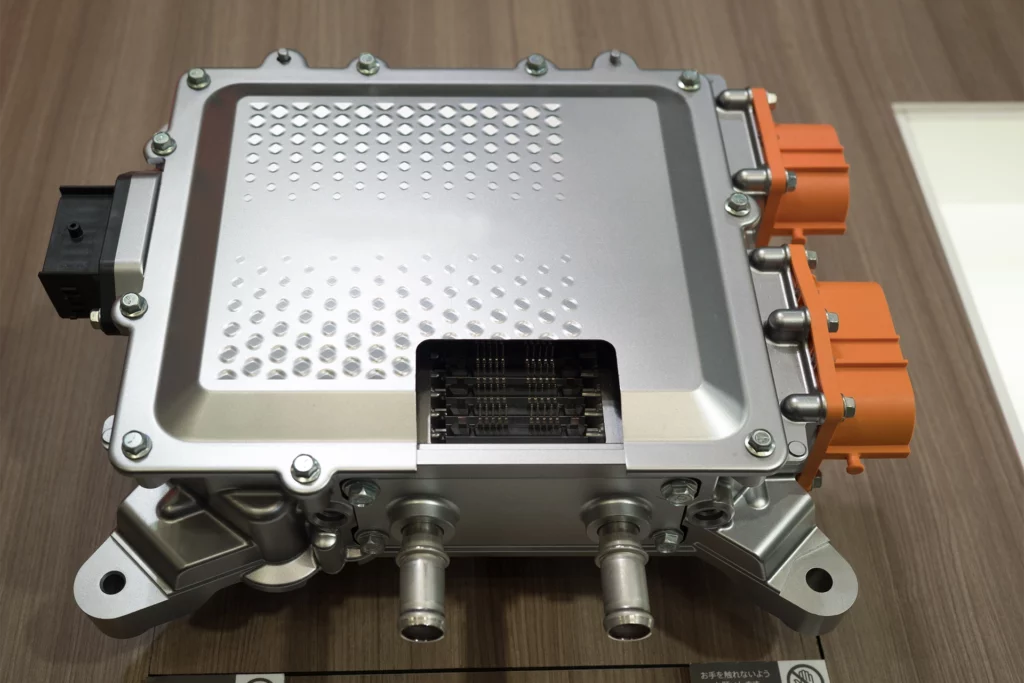
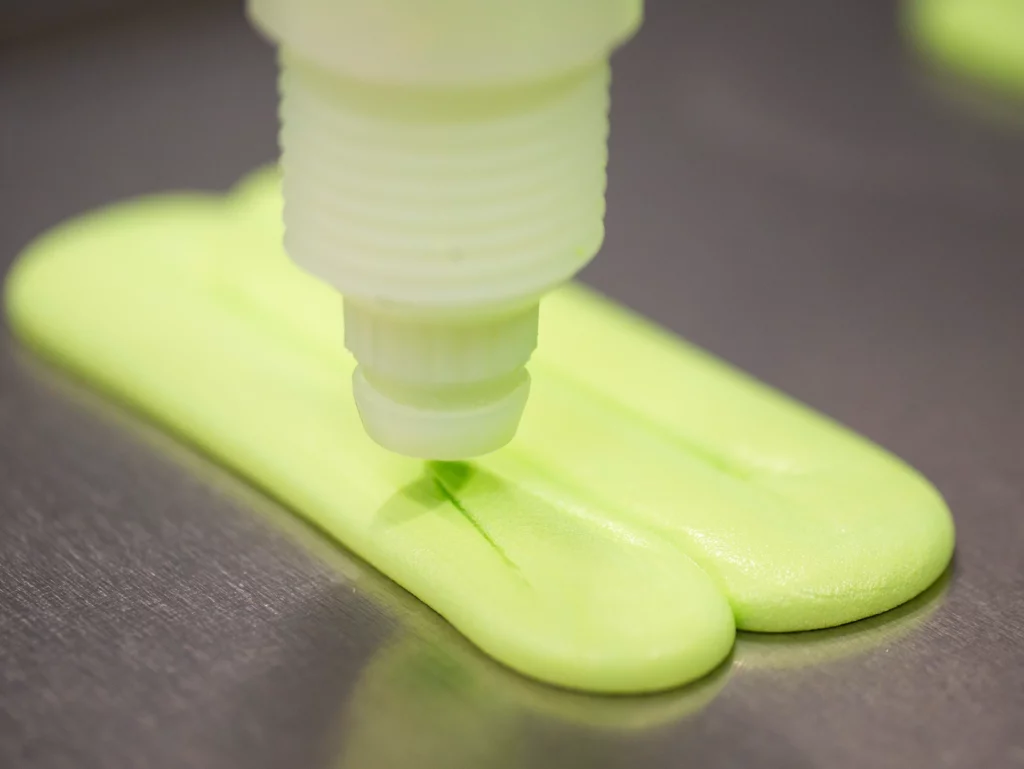
DC/DC Converter
Inverter
Neben der Batterie ist der Inverter (bzw. die Leistungselektronik), welcher zwischen Batterie und Motor sitzt und das Zusammenspiel dieser beiden regelt, das Herzstück des Elektroautos. Der Inverter überwacht und regelt den Elektromotor, ist also für dessen Drehmoment- und Drehzahlsteuerung zuständig. Darüber hinaus wandelt er die Gleichspannung der Batterie, in Wechselspannung um. Das gleiche läuft im Falle des Rekuperierens entgegengesetzt herum – der Wechselstrom des Generators wird in Gleichstrom für den Akku umgewandelt. Viele deutsche Hersteller und Zulieferer sind in diesem Segment führend und arbeiten gerade an der Umsetzung der 800V-Technologie, welche sich künftig durchzusetzen scheint. Neben den ohnehin schon anspruchsvollen Anforderungen an die Kühlung der Leistungselektronik, erfordert die 800V- Technologie eine sehr hohe elektrische Isolationsfestigkeit.
Für die Anbindung der Leistungselektronik an den entsprechende Kühlkörper (z.B. Gehäuse) werden Thermal Interface Materials eingesetzt, gerade die Gap Filler Liquids und Gap Pad Serie der KERATHERM® Produktreihe eignet sich hierfür besonders gut. Für die Kapselung kompletter Baugruppen können auch Produkte der KERAMOLD® Serie zum Einsatz kommen.
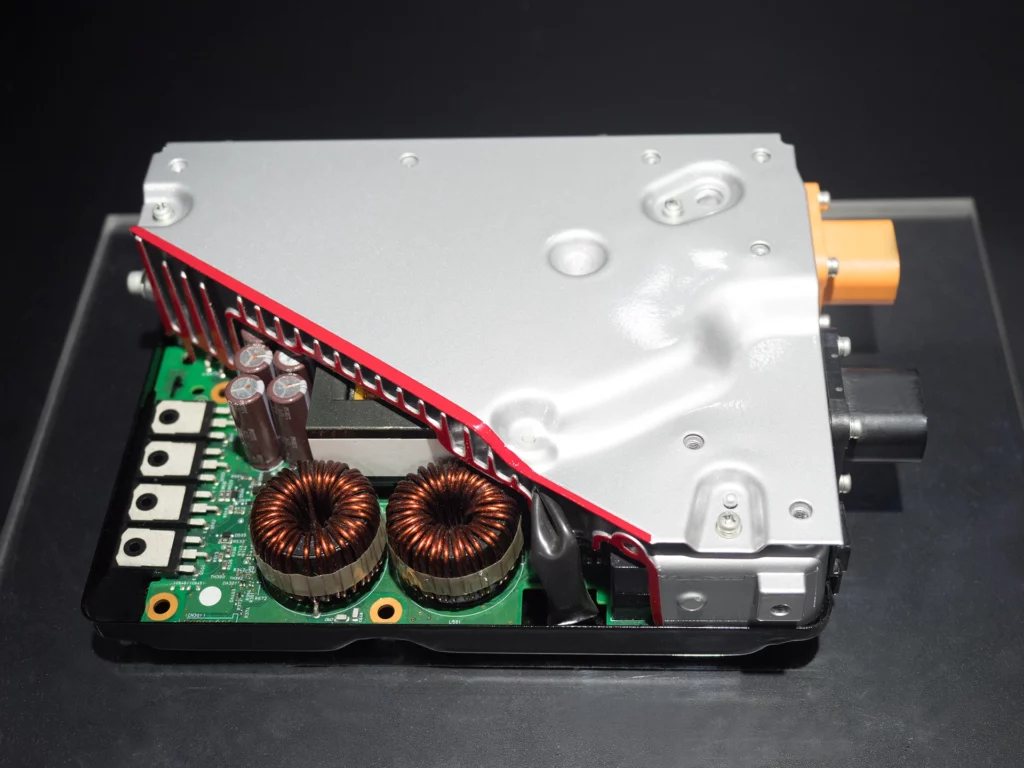
Lösungen
für Power Conversion
Elektrische Heizer
Während bei Fahrzeugen mit Verbrennungsmotor ausreichend Abwärme vorhanden ist, bedarf es bei elektrisch betriebenen Fahrzeugen eines zusätzlichen Heizsystems. Hierbei kommen, neben dem Hochvoltheizer für den Fahrerraum an sich, auch „elektrische Zuheizer“ (12V) für das Thermo Management der Batterie zum Einsatz, ein wichtiger Bestandteil zur Reduzierung der Reichweitenverluste.
Deutsche Hersteller sind in dem Segment der Hochvoltheizer, welche in der Regel für eine 400V oder 800V Architektur ausgelegt sind, marktführend. Auch wenn sich die Konzepte zum Teil unterscheiden, in beiden Fällen entscheidet auch das entsprechende Thermal Management über die Effizienz und Verlässlichkeit der Baugruppe.
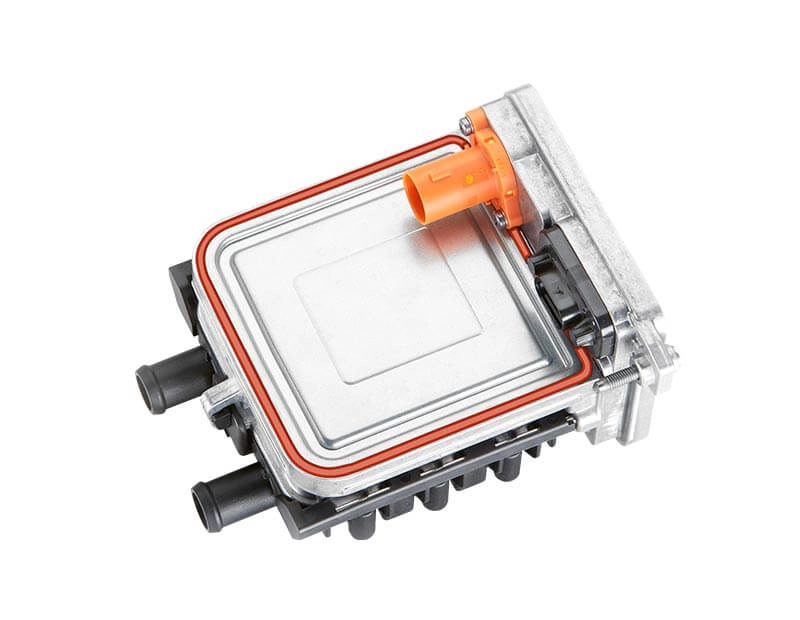
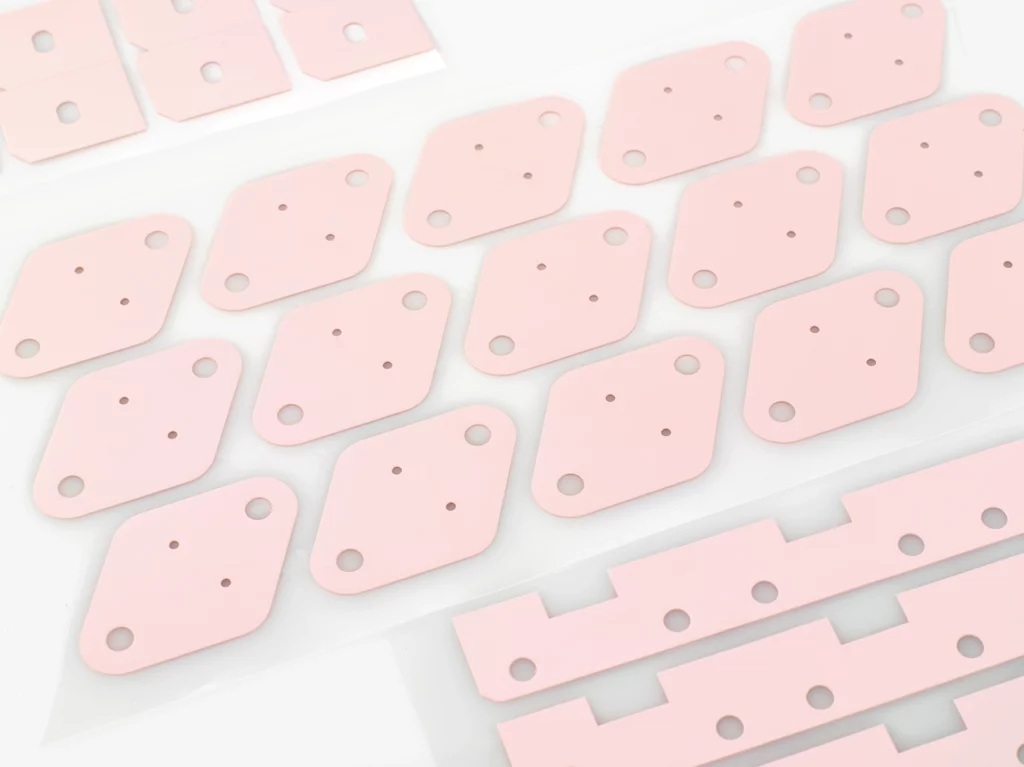
Für die Anbindung der Leistungselektronik an den entsprechende Kühlkörper (z.B. Gehäuse) werden Thermal Interface Materials eingesetzt, gerade die Gap Filler Liquids und Gap Pad Serie der KERATHERM® Produktreihe eignet sich hierfür besonders gut. Für die Kapselung kompletter Baugruppen können auch Produkte der KERAMOLD® Serie zum Einsatz kommen.
Lösungen
für Elektrische Heizer
Service
- Dispensing
- Spritzguss
- Vereinzelung
Produkte
eBikes
Die Elektrifizierung von Fahrrädern ermöglicht vielen Leuten eine neue Form von Mobilität, sowohl im Alltag als auch in der Freizeitbeschäftigung. Neben der Integration des Elektromotors spielt auch das Batteriemodul inklusive intelligenten Batterie Management System (BMS), welches die Batterie vor Schäden schützt, eine entscheidende Rolle in Bezug auf den Fahrkomfort. Die Anforderungen an die zusätzlichen Komponenten sind klar definiert:
- Geringes Gewicht, geringer Platzbedarf
- Energieeffizienz - Hohe Reichweite
- Hohe Zuverlässigkeit und Langlebigkeit
- Geräuscharmer Betrieb
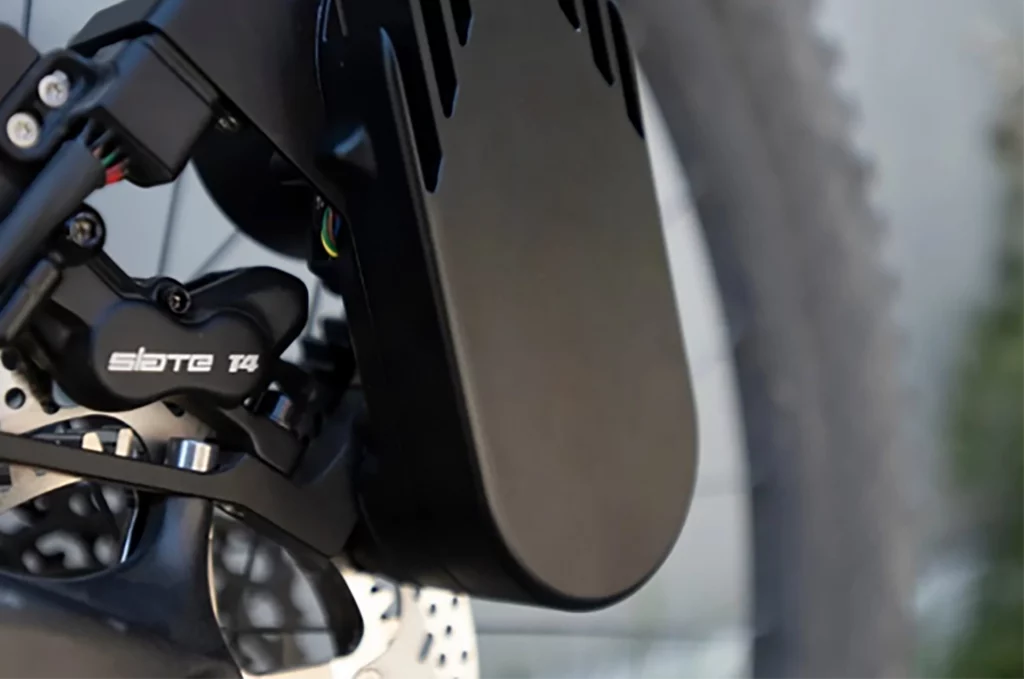
und Antrieb
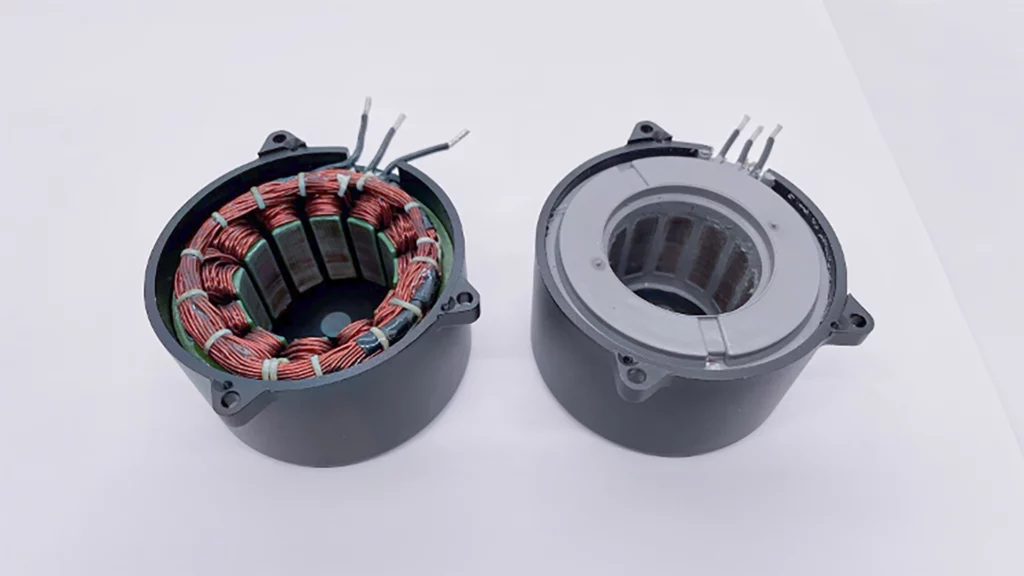
umspritzter Elektromotor
Das BMS bzw. die Leiterplatte inkl. Halbleiter wurde bisher in vielen Fällen mit einer „Conformal Coating“ Schicht versehen, um kritische Bauteile vor Staub, Schmutz und Feuchtigkeit zu schützen. Durch die höheren Leistungsanforderungen an die Platine bedarf es einer entsprechenden Lösung zur Wärmeabfuhr. Hierfür sind zum einen die Produkte der KERATHERM® Reihe hilfreich. Mit diesen Zwischenlagenmaterialien (Therma Interface Materials) in Form von Folien oder Pads kann die Wärme von Wärmequelle zu Wärmesenke (z.B. Gehäuse) effektiv geleitet werden. Produkte der KERAMOLD® Serie schützen sowohl die Elektronik (vergleichbar wie im Falle des Conformal Coatings) und verfügen gleichzeitig über die wärmeleitende Eigenschaft einer Wärmeleitfolie – eine „all in one“ Lösung.
Auch im Falle des Elektromotors können die Produkte der KERAMOLD® Serie eine echte innovative Lösung darstellen. Während Elektromotoren bisher mit gering wärmeleitfähigen Potting Material vergossen werden, erzielt das Umspritzen desselbigen mit wärmeleitfähigen Spritzgussgranulat denselben Effekt, nur unter deutlich gesteigerter thermischer Performance. Durch die Weichheit des verwendeten Polymers können Vibrationen und auch Geräusche ausglichen und gedämpft werden, was wiederum den Fahrkomfort erhöht. Aber auch die neue Gap Filler Reihe der KERATHERM® Serie ist eine leistungsstärkere Alternative zu konventionellen Potting Materialien.
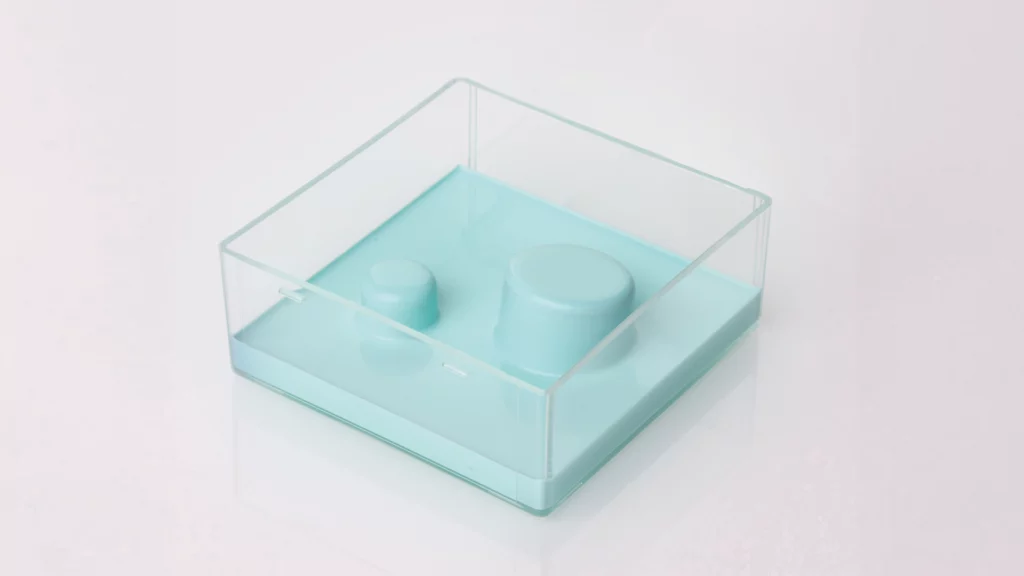
Case Study
Erfahre mehr über die Leistungssteigerung eines eBike Elektromotors mithilfe der KERAMOLD® Produktreihe
Lösungen
für eBikes
LED
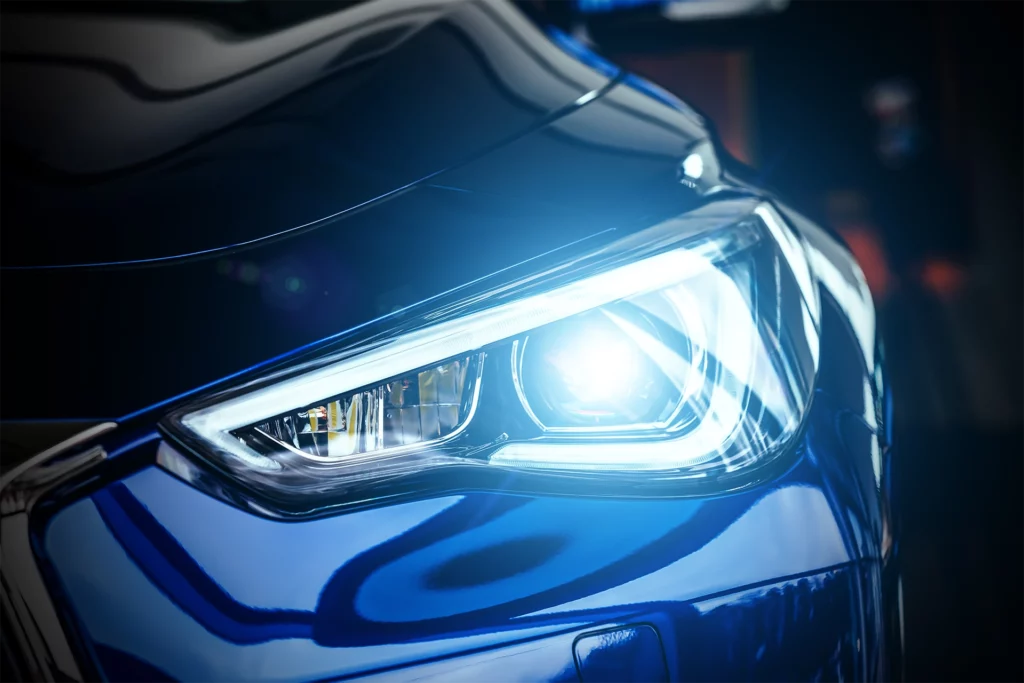
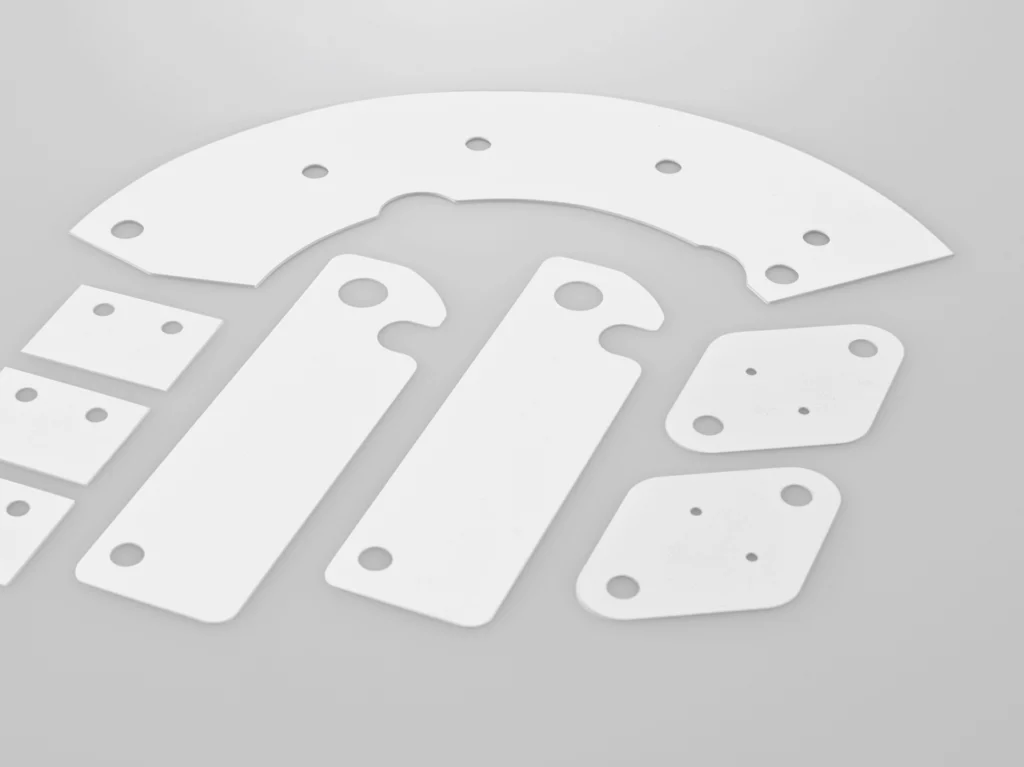
Lösungen
für LEDs
Service
- Dispensing
- Spritzguss
- Vereinzelung